Sealless Direct Drive Pumps
Iwaki America’s Sealless Direct Drive Pumps offer an outstanding balance among size, efficiency and performance. Integrating the motor and pump end into one assembly eliminates concerns about motor bearing life. Our expertise in hydraulic design enables Iwaki America to offer OEM system designers the flexibility of a DC-powered design with controllability and advanced hydraulics.
Our NRD Series pumps are manufactured in adherence to ISO 9001/14001 quality standards and can achieve a maximum capacity of up to 18.5 GPM. They feature a sealless design, which helps prevent leakage in various applications. Our Sealless Direct Drive hydraulic pumps can exceed 25K hours.
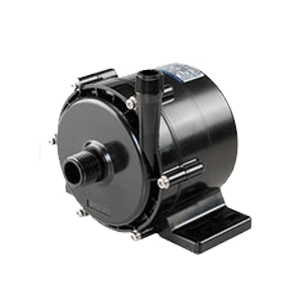
NRD Series
Up to 18.5 GPMNRD Series
24 VDC Pumps
Max. Capacity:
Up to 18.5 GPM
Max. Head:
62.3 ft
Working of Sealless Direct Drive Pumps Explained
A sealess direct drive process pump features an assembly comprising an integral pump and motor assembly, including driver electronics. Similar to a magnet drive design, these pumps do not feature an external drive magnet mounted to a motor shaft, which often transmits the motor torque to the internal driven magnet assembly. Instead, the torque is transmitted directly by a brushless DC motor (BLDC).
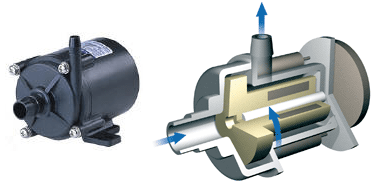
The inner rotating magnet assembly is positioned as the rotor of a motor. The motor windings are wound around the rear housing. The inner rotating magnet assembly is driven by the rotating magnetic field of the BLDC motor. Commutation is performed electronically using sensors to detect the position of the inner rotating element. The driver users the sensor inputs to energize the motor windings. The induced magnetic field drives the inner magnet assembly. This design eliminates the need for a separate motor armature, motor bearings, drive magnet mounted to the motor shaft, and shaft seals. As with magnet drive designs, the Direct Drive sealless structure also eliminates leaks and problems involving seal replacement. Our Sealless Direct Drive OEM pumps are used in applications where regular pumps fail to function. They are compact-sized, efficient and assure a long service life.
Installation of Sealless Direct Drive Pumps
Installation and maintenance of sealless direct drive process pumps require attention to detail and several careful considerations. The tips given below will aid you during installation and maintenance.
- Find the Most Suitable Location for Installation: It is always better to install the pump in a location with sufficient ventilation, and free from chemicals, vapors, dust, and corrosive fumes. As the pump is self-heating, installing it in a ventilated location would help avoid failure due to excess trapped heat. Next, place the pump in the level position, which is free from vibration. If the right level position is not chosen, the output may be affected.
- Choose the Right Mounting Position: Our Sealless Direct Drive pumps are not designed for self-priming, so, they must be installed to lie lower to the liquid level in the supply tank. Ensure to keep the liquid level 30cm higher than the tank outlet. This is because air reaches to the suction and may affect the bearings. Do not mount these pumps in a vertical position.
- Follow the Installation Instructions Carefully: Every Sealless Direct Drive OEM pump requires a different installation. So, if you are using our NRD or DDC series Sealless Direct Drive pump, you must read our installation steps carefully. Ensure you use the right electrical connections, alignment, and mounting accessories.
- Choose a Proper Foundation: The pump must be mounted on a level or stable foundation. Use base plates or proper mounting pads to ensure a vibration-free installation.
- Secure Connections: All the pump connections must be secured, and you can ensure these by double-checking piping, fittings, power supplies, and wiring. Any loose connections can lead to vibration, leaks, or electrical issues.
Maintenance Solutions for Possible Issues of Sealless Direct Drive Pumps
The pump maintenance and inspection must be carried out following the manufacturer’s instructions. The following are some reasons for possible damage or failure of these pumps, along with maintenance solutions. This would be helpful if you use any of our Sealless Direct Drive hydraulic pumps.
-
- The pump is heating up abnormally.
Possible Causes: This could be due to any of the reasons, such as:
- The pump is heating up abnormally.
-
-
- Too high viscosity or specific gravity of the liquid to be pumped
-
- Locked-up motor circuit failure
-
- Ambient temperature or the liquid out of spec
Solution: Pump replacement is only option for most of these causes. However, we recommend you to get in touch with our team immediately if you notice any of these causes.
- Ambient temperature or the liquid out of spec
-
-
- The pump is not running properly.
Possible Causes: This could be due to any of the following reasons, such as:
- The pump is not running properly.
-
-
- Wrong wiring
-
- Very high viscosity or specific gravity of the liquid
-
- Short power capacity
-
- Locked up motor is locked circuit failure
-
- Frequent ON/OFF
Solutions: If you could identify any of the above reasons, then you must take appropriate steps towards the solution. For instance, in case of wrong wiring, you should get it rectified immediately; for locked up motor, contact us immediately; if the specific gravity or viscosity is high then use a more appropriate pump; check the power capacity if you think it is short; and avoid frequent ON/OFF.
- Frequent ON/OFF
-
-
- The delivery head is too low.
Possible Causes: This could be due to any of the following reasons, such as:
- The delivery head is too low.
-
-
- Air trapped in the pump
-
- Loosened pump head mounting screws
-
- Dry running
-
- Air entrained in the suction line
Solutions: If you observe any of the above reasons, ensure you take appropriate steps like expelling air from the pump; tighten the mounting screws by 1.6 Nm; check for dry running before the operation.
- Air entrained in the suction line
-
-
- The pump is leaking.
Possible Causes: This could be due to the loosened pump head mounting screws.
Solutions: You can tighten the mounting screws by 1.6 Nm.
- The pump is leaking.
Applications of Sealless Direct Drive Pumps
Here are some applications of Sealless Direct Drive process pumps.
- Medical Equipment: These pumps are used in liquid transfer and circulation in a variety of analyzer equipment.
- Thermal Management: The pumps are used to heat or cool equipment.
- Marine and Aquaculture: Sealless Direct Drive hydraulic pumps are used in various marine applications to ensure water management and proper water circulation. Fish farming, bilge pumping, ballast systems, and aquarium filtration systems are some applications that utilize these pumps.
Our NRD Series pumps are used in various water pumping applications across industries. Consider Iwaki America Sealless Direct Drive OEM pumps for your pumping application. Get in touch with our team today to discuss your requirements. We would be happy to answer your questions and help you with the right selection.
Videos